We deliver worldwide.
Please contact us for delivery terms to your country
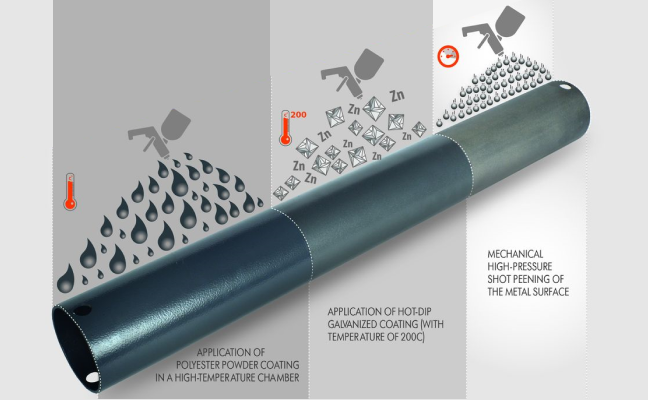
KPRO-7 is a technology for preparation and further powder coating of metal parts of sports equipment.
The technological process of KPRO-7 has been developed and tested by specialists of the KENGURU.PRO Company.
The KPRO-7 protection of metal against corrosion and improvement of visual qualities consists of the following stages:
1. Shot peening
Shot peening involves exposure of the surface of a part to abrasive material, supplied at high speed by the air flow. To carry out such work, special equipment – shot peening machines – is used. The power of the supplied abrasive air flow allows to remove various impurities and coatings, rust, dross, irregularities, and much more.
The processing with shot peening gives a rough, clean surface, which provides good adhesion to the applied materials.
Preparation of the metal is the mechanical removal of the rusting upper layer from bleach-cleaned cast iron or steel with metal shots, at a pressure of 0.5-0.6 MPa for 3-5 minutes. The recommended surface profile of the Rz is from 30 to 50 μm. On the surface of the products, unevenness is formed in the form of depressions, which provide maximum adhesion to subsequent layers of coating. Abrasive peening of the metal surface is performed to grade 2 according to GOST 9.402 (Sa 2 1/2 or Sa 2 of ISO 8501-1.)
Technical characteristics of shot peening line
DC1503-4.11 F82601
1. Size of the input window; 610×1600 mm.
2. Conveyor speed; 0.8-3.2 m/min.
3. Cleaning speed SA 2.5; 1.6 m/min.
4. Turbine type B-306-ADC; 4 pcs. (2 top, 2 bottom).
5. Turbine performance; 220 kg/min.
6. Turbine engine power; 11 kW.
7. Cast steel shot; S330/SS1.0mm.
8. Chipped steel shots; GP025/SS1.0mm.
9. Hardness of steel shot inside; 40-51 HRC
2. Application of zinc-containing coating
Not later than 40 minutes after shot peening, the products are placed in a chamber where the anticorrosive zinc-containing coating (TU 2312-022-12288779-2000) is applied through high-pressure (air) spraying, at temperatures ranging from +10°C to +40°C and relative air humidity of no more than 85%.
Characteristics of zinc-containing coating
Color and appearance – gray (the shade is not normalized), matte, smooth, without foreign impurities
Thickness of one layer is 40-80 μm
Impact strength – not less than 50 cm
Elasticity at bending – not more than 10 mm
Adhesion (according to GOST 15140, method 2) – not more than 1 point
Temperature resistance – 150°С
Density – 2.80-3.00 g/cm3
Mass fraction of nonvolatile substances is 84.0-87.0%
Viscosity – thixotropic
3. Drying process
According to GOST 19007 drying time to grade 3 at a temperature of (20 ± 2)°С and relative humidity of air (65 ± 5)% – no more than 4 hours
Powder coating KPRO-7 (KPRO-7)
Powder coating is applied through electrostatic spraying. It is consists of application of an electrostatically charged powder to a grounded product using a pneumatic atomizer.
First the powder material is poured into the feeder. Through the porous bulkhead of the feeder, air is supplied under pressure, which moves the powder into a suspended state, forming the so-called “fluidized layer” of the coating. Then the aerosol is taken from the container by means of an air pump (ejector), diluted with air to a lower concentration and fed to a sprayer, where the powder coating gets electrostatic charge due to friction. With the help of compressed air, the charged powder paint is applied to a neutrally charged surface, settles and is held there by electrostatic attraction. At the final stage of powder coating, the powder applied to the product is melted and polymerized in the polymerization chamber. Fusion and polymerization occurs at a temperature of 150-220°C for 15-30 minutes, after which the powder paint forms a membrane (polymerizes). At the end of the polymerization, the product is cooled with air.
Only polyester powder, resistant to aggressive environment, is used. This type of paints does not include toxic TGIC. Referring to the Interpon D series architectural powder coatings, the Interpon D1036 series provides excellent resistance to environmental influences, preserves the original color of the coating and meets all major European standards in this field.
Particle size – Suitable for tribo and electrostatic deposition methods
Density of 1.2-1.85 g / cm3,
Solidified state*
20 minutes at 170°C
15 minutes at 180°C
10 minutes at 190°C
Mechanical tests
According to GOST 19007 drying time to grade 3 at a temperature of (20 ± 2)°С and relative humidity of air (65 ± 5)% – no more than 4 hours
POWDER COATING KPRO-7 (KPRO-7)
Powder coating is applied through electrostatic spraying. It is consists of application of an electrostatically charged powder to a grounded product using a pneumatic atomizer.
First the powder material is poured into the feeder. Through the porous bulkhead of the feeder, air is supplied under pressure, which moves the powder into a suspended state, forming the so-called “fluidized layer” of the coating. Then the aerosol is taken from the container by means of an air pump (ejector), diluted with air to a lower concentration and fed to a sprayer, where the powder coating gets electrostatic charge due to friction. With the help of compressed air, the charged powder paint is applied to a neutrally charged surface, settles and is held there by electrostatic attraction. At the final stage of powder coating, the powder applied to the product is melted and polymerized in the polymerization chamber. Fusion and polymerization occurs at a temperature of 150-220°C for 15-30 minutes, after which the powder paint forms a membrane (polymerizes). At the end of the polymerization, the product is cooled with air.
Only polyester powder, resistant to aggressive environment, is used. This type of paints does not include toxic TGIC. Referring to the Interpon D series architectural powder coatings, the Interpon D1036 series provides excellent resistance to environmental influences, preserves the original color of the coating and meets all major European standards in this field.
Particle size – Suitable for tribo and electrostatic deposition methods
Density of 1.2-1.85 g / cm3,
Solidified state*
20 minutes at 170°C
15 minutes at 180°C
10 minutes at 190°C
Chemical tests and tests for durability of coating
Salt mist – passed ASTM B117 (1000 hours) without traces of detachment beyond 3 mm from the cut.
Sodium salt – ISO 9227 (1000 hours), peeling <16 mm2/10 cm
Wet chamber – passed BS3900-F2 (1000 hours) without detachment and loss of gloss
Sulphur dioxide – passed ISO 3231 (Kesternich) without detachment beyond 1 mm from the cut, without color change and bubbling after 24 cycles
Immersion in distilled water – passed BS3900-F7 (240 hours) without detachment and loss of gloss
Durability when used outdoors – the product is characterized by its high performance level. A slight uniform loss of gloss is possible without damage to the coating. Melting is virtually non-existent – within ASTM D659: 1980
Accelerated test for atmospheric stability – Sun test Original Hanau Quartzlampen ISO 11341. Retention of >50% of gloss after 1000 hours
Chemical resistance – normally high resistance to all low concentrated acids and alkalis, as well as oils at normal temperature.